Are you Managing your Supply Chain… or Hoping for the Best?
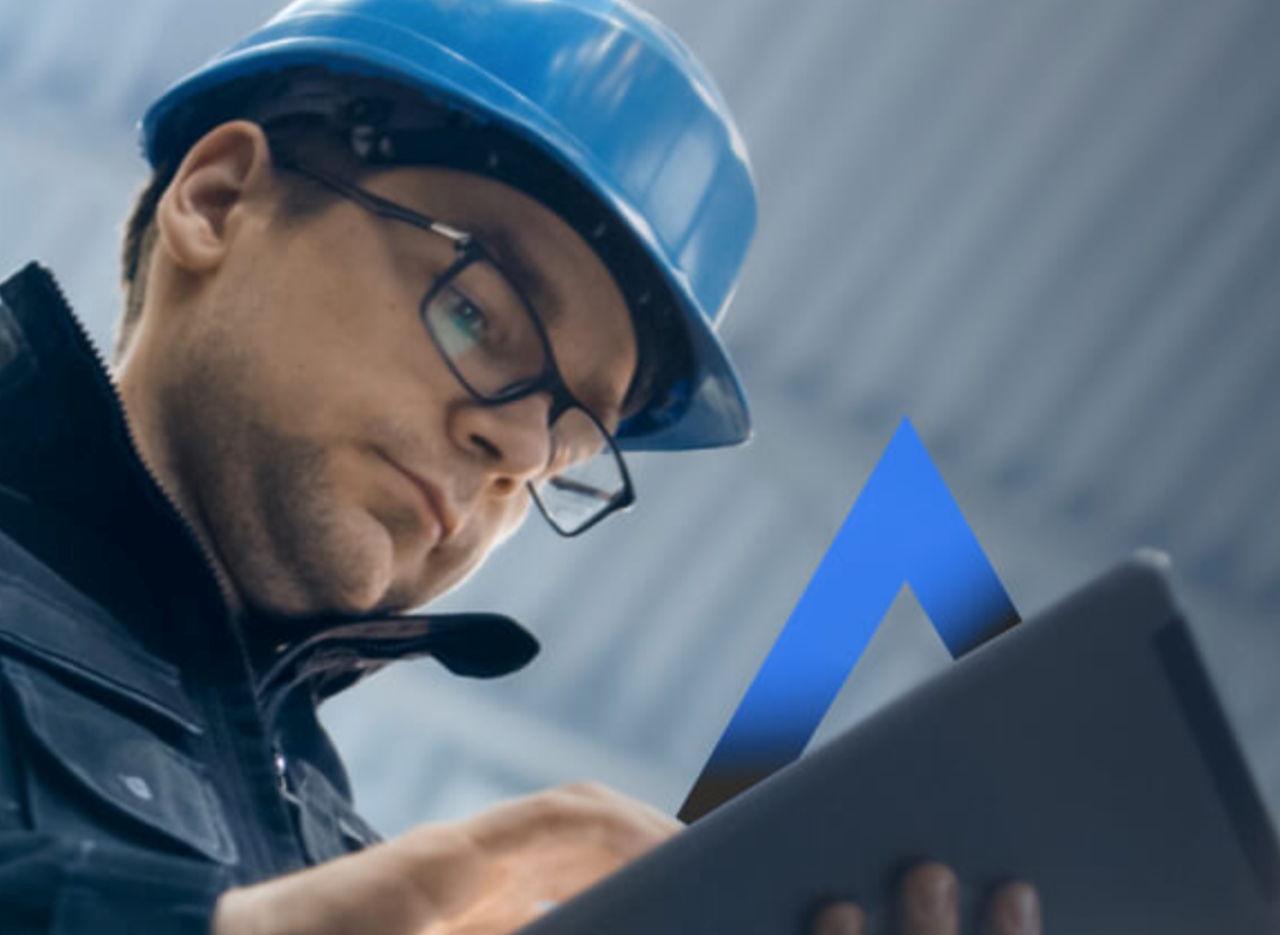
Ctrl Hub’s Managing Director, Mark Lisgo describes how digital solutions can provide the key to more effective and proactive Supply Chain and Contractor Management.
It is all too easy to take your supply chain for granted. When operations are running smoothly, it seems far important to hit the next target, close the next deal, or focus on that upcoming project.
You would like to think that your suppliers (and your customers for that matter) operate to the same high standards. That they strive for the same high quality product or output every single time.
You have an expectation that they have the same commitment to health and safety as you. They have proper procedures and systems in place. All of their workers are suitably trained, qualified and competent to perform the task in hand.
You might assume that they have the same level of integrity as you. They do not cut corners. They put their hands up and accept liability for their own actions or omissions.
Far too often, however, you will only discover that all is not as you had hoped. Unfortunately, that discovery generally happens once an incident has occurred, or an unsatisfactory outcome has arisen. Instead of proactively addressing issues, damage limitation – finger pointing – becomes the required course of action.
According to the HSE, in the United Kingdom in 2017/18 there were:
- 144 fatal injuries to workers;
- 555,000 self reported injuries at work; and
- 71,062 non-fatal injuries reported under RIDDOR
(Source: Health and Safety Executive Report – Health and Safety at Work 2018)
Hoping for the best is not an acceptable course of action. Injuries and incidents are going to occur.
You can have the most detailed, thorough vetting procedures and pre-qualification exercise in the world. All that gives you is a snapshot of the position prior to commencement of a contract. If the supplier questionnaires are filed away, never to be looked at again, they quickly become obsolete. Continuously updating those files is a laborious and time-consuming task – and is therefore expensive.
Say an accident occurs on site, or out in the field. Your admin and legal teams will go into panic mode, hunting for the relevant PQQ, requesting updated information. Hoping that the relevant qualification or certification is still in date, and that the proper risk assessments and processes have been implemented.
Contractual liability should, in theory, flow through the supply chain and sit where the problem occurs. This is not always the case. If a supplier (or its lawyers) can see a potential avenue toward avoiding or reducing a liability, they will almost certainly look to take it. A party who has suffered injury or financial damage will not necessarily look to the person most culpable. They will seek the person with the deepest pockets or the person with the reputation to protect.
Reputational damage rarely passes down a supply chain in the same way that contractual liability would be expected to flow. The bigger the name, the bigger the reputation and the bigger the target for all those who might look to take a go – be it injured parties, press, the general public or regulators. You can point to the supplier who was at fault, but Joe Bloggs Limited does not capture attention in anywhere near the same way as a household name client or a tier one contractor.
The world we live in has changed enormously over the past twenty years. We have instant access to news and information. We demand real time data. It is becoming less and less acceptable or defensible to simply point the finger down the supply chain and say “it was their fault, we thought everything was fine”.
It is also no longer acceptable to say “I prefer using paper” or “this is how we have always done things”. Your competitors will not tolerate this from their workforce.
Digitisation is key to proper supply chain and contractor management – unless you are prepared to dedicate a team of admin staff (and the huge cost that entails) to continually request and monitor supplier information. Why not redirect your human resources to tasks and projects that will generate revenue?
Technology provides an audit trail that can evidence that things have been done properly, and are being done properly. It provides factual evidence. It removes guesswork, doubt and wriggle room.
Real time data capture and real time reporting allow you a far greater understanding of how your supply chain is performing. You can respond instantly to issues as they arise, instead of having to scramble after damage has already been done.
By proactively managing your supply chain, you can influence and guide how they perform. You can promote best practice and efficiency that enables them to perform better and more cost effectively. You can significantly reduce risk. That all benefits everyone involved.
Few things are certain in these fast paced times. This, however, I am prepared to say with total certainty. Companies who embrace digitisation will thrive against those who are unwilling to accept or face change. You must move ahead, or you will ultimately cease to exist.
To learn more about how Ctrl Hub can support you to manage your supply chain more effectively please visit our website in the first instance www.ctrl-hub.com